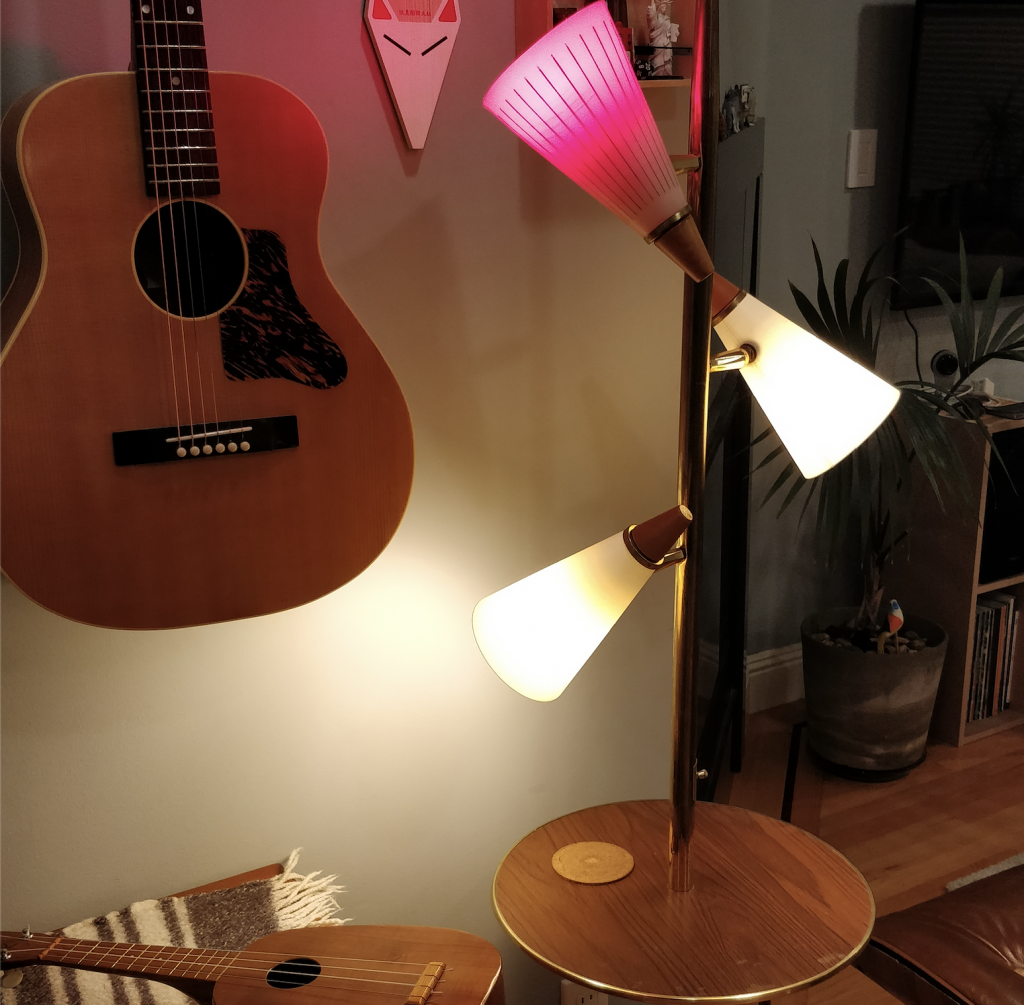
I’ve had this mid-century pole lamp that’s been sitting in disrepair. The plastic (?) cone lampshades started disintegrating and one day a friend was over, reached up to adjust one and it exploded and shattered in his hand. Game over. No one makes replacements for these.
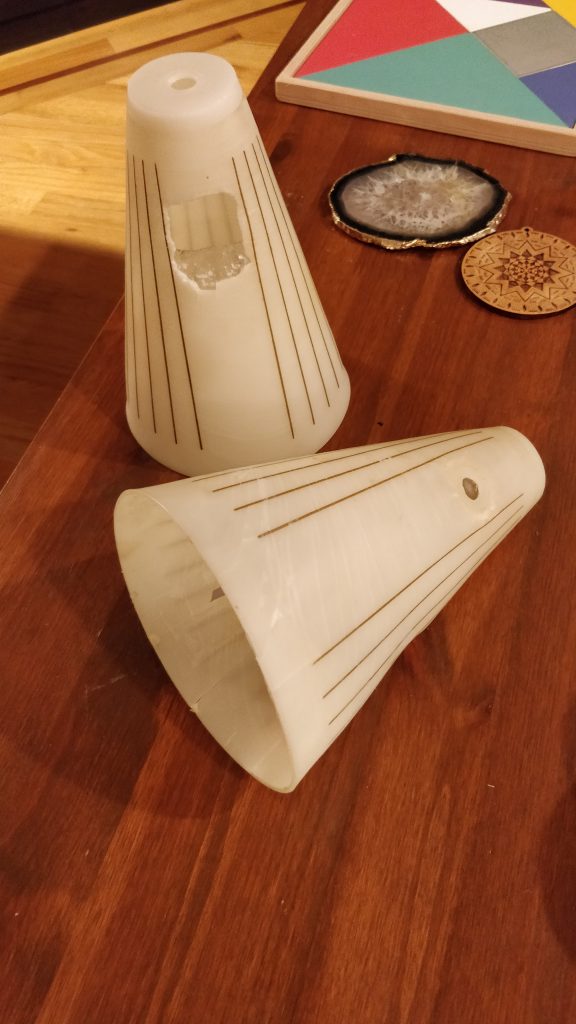
It has long been on my list of things to fix with 3D printing but I had some technical limitations. First I had to get a printer that was big enough to print the shade, which I finally did (thanks, Craigslist Creality Ender 3!). Secondly, I had to take the thing apart, which was the real challenge. I left it half-assembled for years before I finally got tired of looking at it and spent an hour figuring it out.
As it turns out you have to disassemble the whole thing down to the base, then pull the wires out of the tubing where they connect at a plastic screw wire terminal connector. Detach it from there, then pull the entire pair of wires out through the joint where the bulb is.
Modeling the actual lampshade was simple, it took no longer than 30 minutes. I just made two circles of the correct diameter, spaced them out with the measured distance, and connected them via a loft. Then I shelled the model with 2mm wall thickness and poked a hole in the sides. Done:
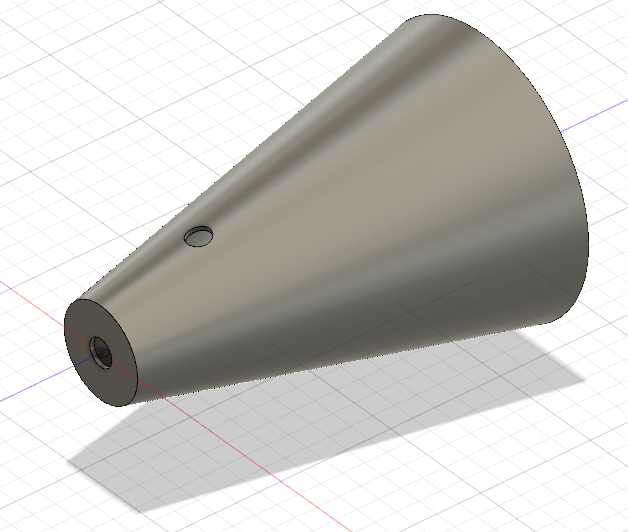
Next printing the thing. The slicer software, Cura, kept doing dumb stuff such as rendering the infill as horizontal instead of circular and adding unnecessary support material. That was adding multiple hours to the print time. I tweaked the wall width and and managed to get the thing to print as strictly concentric circles at a width of 4 lines each layer. I also used the highest layer heigh possible, 0.32mm. This brought the print time down from 10+ hours to 3.5! It pays to tweak these things.
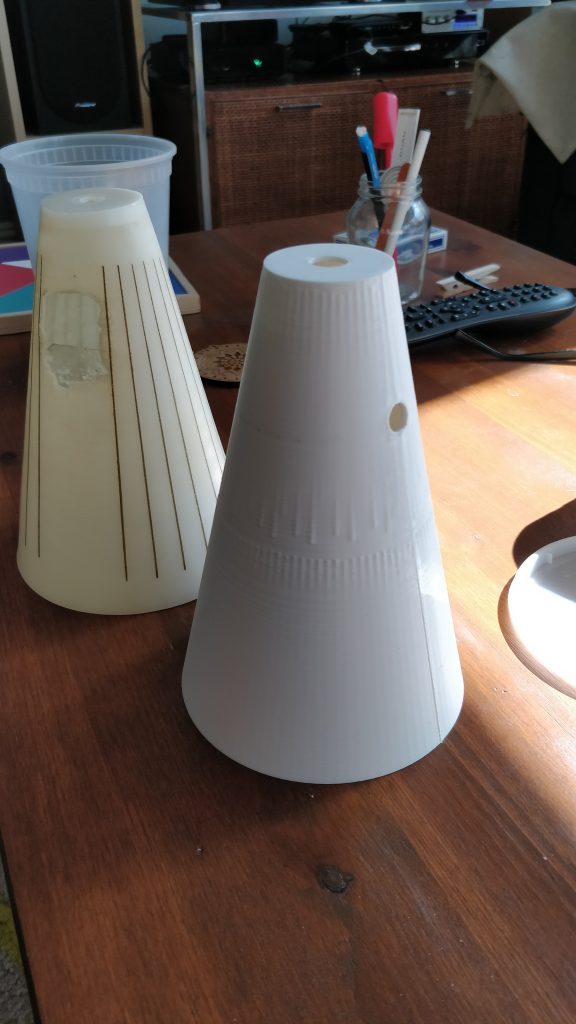
Above is the finished print. You can see some surface imperfections. I really do think these are software/slicer related since they occurred on both in the exact same manner even after servicing the printer in between. But they actually kind of look decorative, so I didn’t bother spending more hours sanding them down.
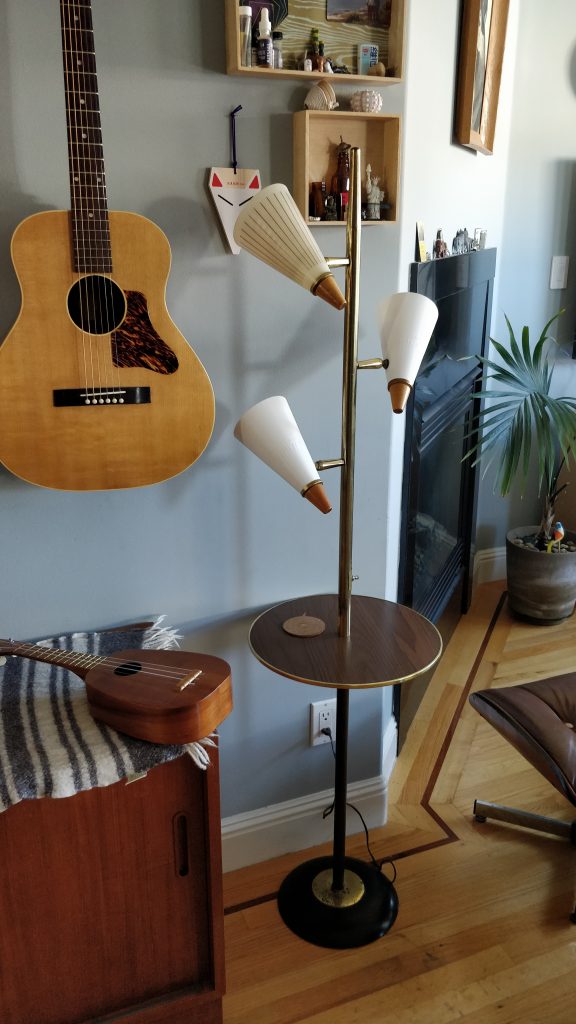
And here is the whole thing re-assembled. One of the original cones on top is still (barely) intact. Once it goes, no big deal. I’ll print one more.
It sure feels good to fix things and keep them out of the landfill! It’s not a very valuable lamp, so it would have been totally impractical to take to a professional. The perfect use case for DIY and 3D printing tech.
You did a FANTASTIC job with this project! I am currently in the same position. I have my grandmother’s floor lamp (which I love). Two of the 3 shades are damaged, just like yours. I don’t have a 3d printer, but I do have a glowforge…so, I’m trying to figure out what my next steps will be. Not looking forward to taking my lamp apart to fix the shades, though. Ugh. Thanks for the post and being a great example. I hope mine comes out as nice as yours did. 🙂
Thanks! I wish I had more experience with Glowforge, not sure what the approach would be. Perhaps making layers that would be glued together. Though if it’s a cone, maybe you can cut a shape that can be rolled into the proper cone shape. Finding the right material that is both rigid, bendable and translucent might be tricky.
Another option is to outsource the 3D printing to a company like Shapeways. Just send them the model and they do the rest. There might be local businesses that do that too.
Anyone making these I have looked and looked I need help please thanks
I have the same lamp! Different shades though. I am currently searching for a replacement shade.
I purchase some old new stock shades. Now to figure out how to unhook the wires.